Quality Control
Beauty & Health starts with the details
We at MystGem are manufacturing professionals, which is why we have a department specializing in quality control to guarantee the quality of the products that we provide. Our quality control and manufacturing departmentswork in tandem in each and every phase and process, including the hand cutting,shape cutting, shape stone, inspection and packaging process —together they ensure the quality of the final product.
By your side from conception to packaging
Our technical and industrial teams provide a pool of expertise to support you in defining your jade roller & Gua Sha with your brand and packaging project and ensuring perfect compatibility between our packaging and your products and processes, which guarantees our shared success.
We offer one-stop packaging services, backed by packaging experts and more than 20 years of researchin the beauty & heath tools industry.
Every single service is specifically tailored and you’re carefully supported through each phase of the process, from the initial design of the product to after-sales services which were established by MystGem to also provide quality feedback.
Raw Material Checking
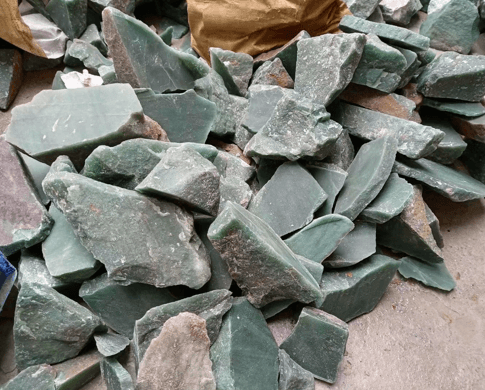
We cooperate with the local importer who do the business of gemstone or crystal, also have the channel in this industry to get the ston raw materials, choose the stone with stable level and the semi-product will be checking and select.
We have more than 30 different Crystal&Gemstone materials which are 100% natural. It can be customized according to the needs of customers.
* Rose Quartz * Tiger Eye
* Blooded Stone * Blue Spot
* Xiuyan Jade * Yellow Jade
* White Jade * Red Aventurine
* Jasper Crinoid * Jasper
* Fluorite * Gold Sandstone
* Green Aventurine * Green Jade
* Grey Agate * Labradorite
* Lapis Lazuli * Picture Jasper
* Opalite * Red Jasper
* Rock Quartz * Ruby Zoisite
* Black Obsidian * Sodalite
* Indian Agate * White Howlite
*Snowflake Jasper * Unakite
Manufacturing Quality Management
initial Inspection
Within the first 3 days of mass production, we must finish the first 10 pieces of final products, which will be inspected in details. If there is any problem, we will immediately adjust the whole production and solve all potential problems at the source.
In this step, we will check every detail carefully according to the original design and the sample, from size, color and more. By doing so, we can avoid possible mistakes and make adjsutment timely.
Random Check
Throughout the whole manufacturing process, we have arranged a quality inspector at every stage, who will check the samples picked out from the production line at random per hour. If there is any defective product, they will be modified or weeded out, the worker who made it will be trained again until she is qualified.
Final production inspection
We know that any defects, even the tiniest one, will damage your brand image in local markets, and we will work tirelessly to prevent this from happening.
We will arrange10 experienced QA to conduct 100% inspection by checking all stone piece by piece to ensure no detail will be missed and minimize the possibility of mistakes extremely.
For the safety of user, we also have the staff to use the jade roller & Gua Sha to touch it and feel the smooth.
Focus on the details
At MystGem factory, quality is at the heart of our development. We allow our clients to confirm sample & product quality three or four times on average to ensure a perfect beauty & Massage tools solution. We believe in our quote – quality makes better sales, better life, better you and me. Quality borns in a clean and well-managed process. Face roller / Guasha sets are in direct contact with the human body. If we compromise to lower cost or more profit, we will make eyelash business no honor. That’s why our quality department understands, implements and maintains, throughout our facilities, all requirements imposed by ISO and our clients. We are an extension to your eyelash quality department, available at all times throughout the completion of your project.
Process to Maximize Your
Added Value
Starseed is committed to offering the very best client service, support, and overall value to our client through the control of high-quality lash materials, wearing experience, and packaging control. Our Quality Management System (QMS) consists of procedures and work instructions to ensure product integrity, reliability, and on-time delivery to meet your specifications and requirements.
We are confident that the service and materials we offer will provide the best solution required for your beauty & Health business.

1. Purchasing process
- Customer needs identification
- Free samples confirmation
- Issuing purchase order

2. Made-to-order
- Pre-production samples manufacturing
- Samples confirmation

3. Manufacturing
- Mass production samples confirmation
- Issuing testing report

4. Delivery
- Transport by ship/train/air.
- Mass products confirmation
- After-sales service
Quality Control Throughout Production
Our integrated approach to quality focuses on process monitoring and regular management review of results across a range of quality criteria
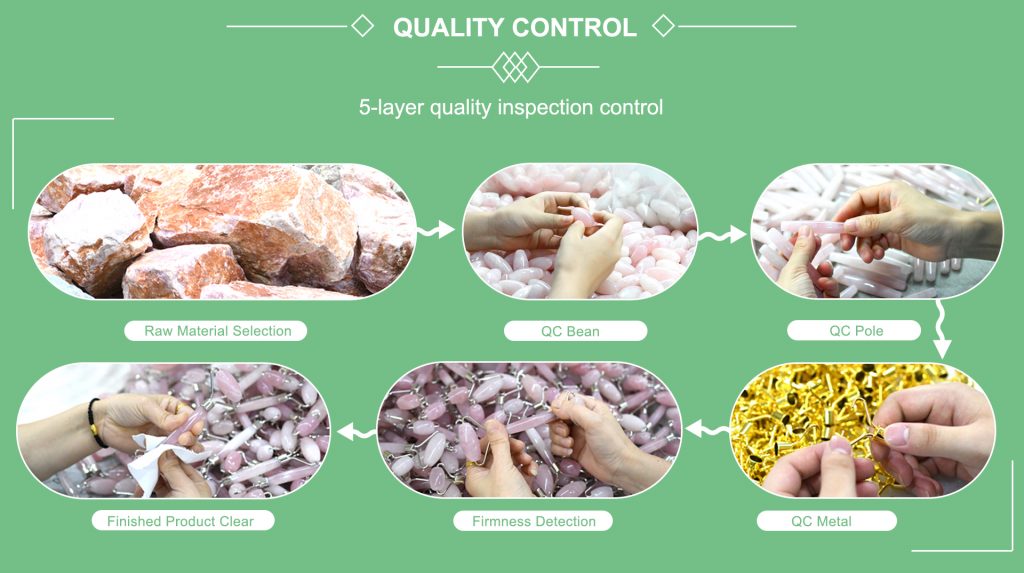
Accessories Checking
How Clients Say About Our Quality
Our success is measured by how our clients feel about their experience with us. View More Reviews